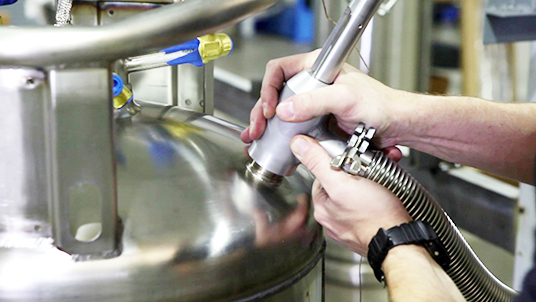
Vacuum technology is an enabling technology for vacuum coating not only because it creates an environment for atomistic deposition process but also because it influences the unit cost, reproducibility, and the functionality of the end product. Vacuum technology began to prosper in the mid-1600s with the invention of manometer/barometer and the piston-type vacuum pumps, many of which were derived from the water pumps used at that time. But today, the application of vacuum technology is particularly crucial to the success of various coating processes.
The vacuum technology helps to create coatings with a high degree of uniform thickness ranging from several nanometers to more than 100 mm while still accomplishing exceptional reproducibility of the coating properties. Moreover, the variety of coating is also very large as in addition to metal and alloy coatings, layers may be produced from several chemical compounds or layers of different materials in sandwiched form. Therefore, one of the significant benefits of vacuum coating over others is that many special coating properties desired, like hardness, structure, electrical conductivity or refractive index, are obtained by just selecting a specific coating method and the process parameters for a specified coating material.
Coating Sources
In all the vacuum technology coating methods, layers are formed by material deposition from the gas phase. The coating material might get formed by physical processes like evaporation and sputtering, or even by chemical reaction.
Thermal Evaporators
In the evaporation process, the material to be deposited is heated to a temperature such that it reaches a sufficiently high vapor pressure and the desired evaporation or condensation rate is set. The simplest source utilized in this process comprises of wire filaments, boast of sheet metal, or electrically conductive ceramics that are heated by passing an electric current through them. However, there is no restriction on the type of material to be heated. Moreover, the chemical reactions between the holder and the material to be evaporated can occur resulting in either a reduction of the lifetime of the evaporator or contamination of the coating.
Electron Beam Evaporators
In this process, the coating material is evaporated using an electron beam gun. The material is kept in a water-cooled crucible and then is bombarded by a focused electron beam and thereby getting heated at the same time. Since the crucible remains cold, contamination of the coating by crucible material is avoided and as a result of which, a high degree of pure coating is achieved. Changing the power of the electron beam, the evaporation rate is controlled very easily and quickly.
Cathode Spluttering
In this process of cathode sputtering, the target, a solid is bombarded with high energy ions in a gas discharge. These high energy ions transfer their momentum to the atoms in the target material, thus knocking the atoms off. These displaced atoms get condensed on the substrate facing the target. But when compared with the evaporated particles, the sputtered particles come with higher kinetic energy. And the best part is that sputtered layers usually come with higher adhesive strength and a much denser coating structure than the evaporated ones.
Chemical Vapor Deposition
In this process, the substance is already in the vapor phase when admitted to the vacuum technology system. In order to deposit the same, the substance must be thermally excited by putting it at a high temperature. Usually, in this type of process, a large number of chemical reactions happen, some of which are taken advantage of in order to control the desired composition and the properties of the coating. For instance, using silicon-hydrogen monomers, soft Si-H polymer coatings can be created by the controlling process parameters.